Complete Overview to Preventing Weld Undercut: Tips and Techniques
Complete Overview to Preventing Weld Undercut: Tips and Techniques
Blog Article
Grasping the Art of Welding: Just How to Prevent Undercut Welding Issues for Flawless Fabrication Outcomes
By comprehending the origin creates of undercut welding and implementing reliable methods to stop it, welders can boost their craft to brand-new levels of quality. In the search of perfect fabrication outcomes, mastering the art of welding to stay clear of undercut problems is not simply a skill however a need for those striving for excellence in their work.
Recognizing Undercut Welding
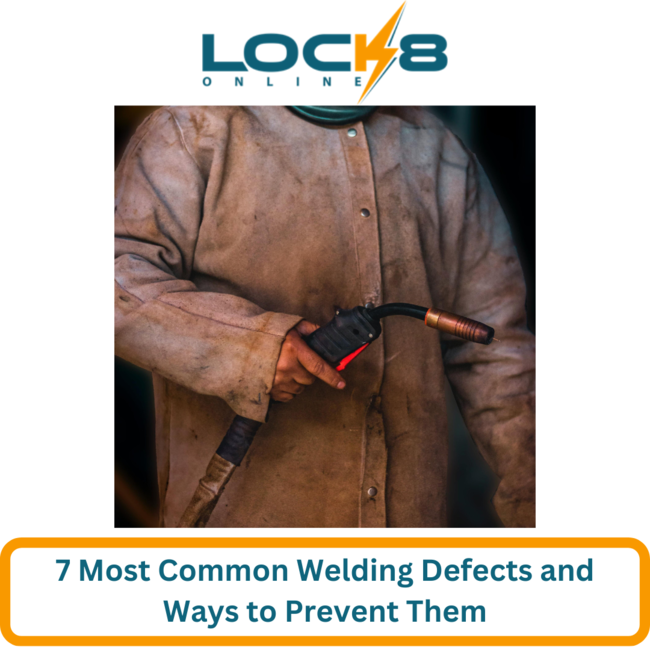
To prevent undercut welding, welders ought to ensure appropriate welding parameters, such as readjusting the existing, voltage, travel speed, and maintaining the right electrode angle. By recognizing the causes of undercut welding and applying preventative steps, welders can achieve high-quality, structurally sound welds.
Sources Of Undercut in Welding
Understanding the factors that add to damage in welding is vital for welders to produce high-grade, structurally audio welds. Insufficient welding incorrect or existing welding speed can additionally add to damage. Comprehending these causes and implementing appropriate welding strategies can aid avoid undercutting problems, making certain strong and durable welds.
Strategies to stop Undercutting

To reduce the danger of damaging in welding, welders can utilize strategic welding strategies targeted at enhancing the top quality and stability of the weld joints. One efficient method is to readjust the welding parameters, such as voltage, present, and take a trip rate, to ensure correct warmth input and deposition. Keeping a suitable electrode angle and making certain constant travel rate can additionally aid protect against undercut. Additionally, making use of the proper welding technique for the certain joint configuration, such as weave or stringer beads, can add to decreasing damaging. Preventing weld undercut.
Furthermore, appropriate joint prep work, including guaranteeing clean base materials without impurities and making use of the ideal welding consumables, is important in avoiding undercut flaws. Employing back-step welding techniques and controlling the weld bead profile can additionally help distribute heat evenly and decrease the Get More Info danger of undercut. Normal examination of the weld joint throughout and after welding, as well as carrying out quality control steps, can aid in attending to and discovering damaging problems quickly. By applying these methods diligently, welders can accomplish perfect construction results with minimal undercut defects.
Importance of Appropriate Welding Parameters
Picking and keeping proper welding specifications is important for attaining effective welds with very little defects. Welding specifications refer to variables such as voltage, existing, travel speed, electrode angle, and protecting gas flow rate that straight influence the welding process. These criteria have to be carefully adjusted based upon the sort of material being welded, its thickness, and the welding method utilized.
Correct welding specifications ensure the correct amount of heat is related to thaw the base metals and filler material uniformly. If the criteria are set expensive, it can bring about too much heat input, triggering distortion, spatter, or burn-through. On the various other hand, if the criteria are also reduced, insufficient combination, absence of penetration, or damaging might occur.
Quality Guarantee in Welding Operations
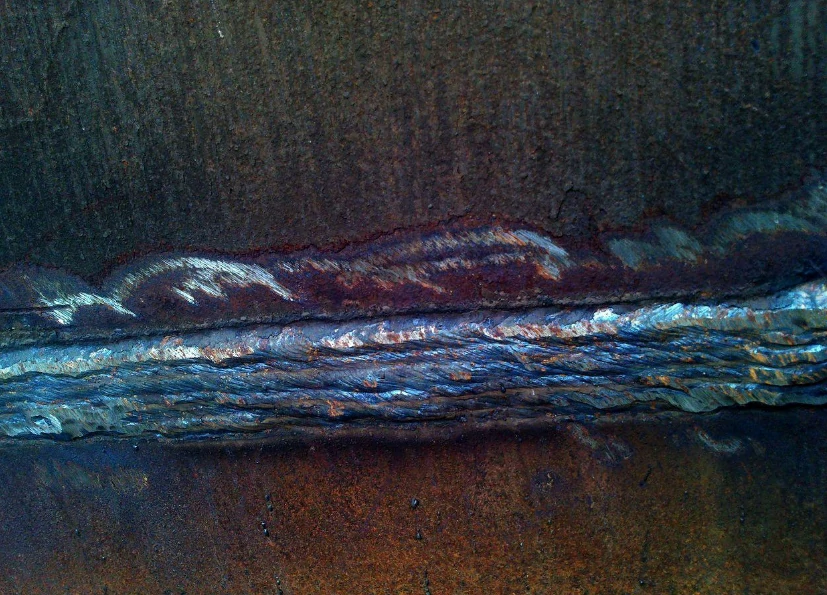
Conclusion
To conclude, grasping the art of welding needs a comprehensive understanding of undercut welding, its causes, and strategies to stop it. By making certain appropriate welding specifications and executing quality go to my blog control methods, perfect fabrication outcomes can be achieved. It is essential for welders to consistently pursue quality in their welding operations to avoid undercut problems and generate high-grade welds.
Undercut welding, a common issue in welding processes, happens when the weld metal does not effectively load the groove and leaves a groove or depression along the bonded joint.To avoid undercut welding, welders need to ensure appropriate welding criteria, such as readjusting the current, voltage, travel rate, and maintaining the appropriate electrode angle. Poor welding current or incorrect welding rate can additionally add to damage.To minimize the threat of undercutting in welding, welders can use strategic welding strategies aimed at enhancing the quality and honesty of the weld joints.In verdict, mastering the art of welding requires a detailed understanding of undercut welding, its reasons, and techniques to stop it.
Report this page